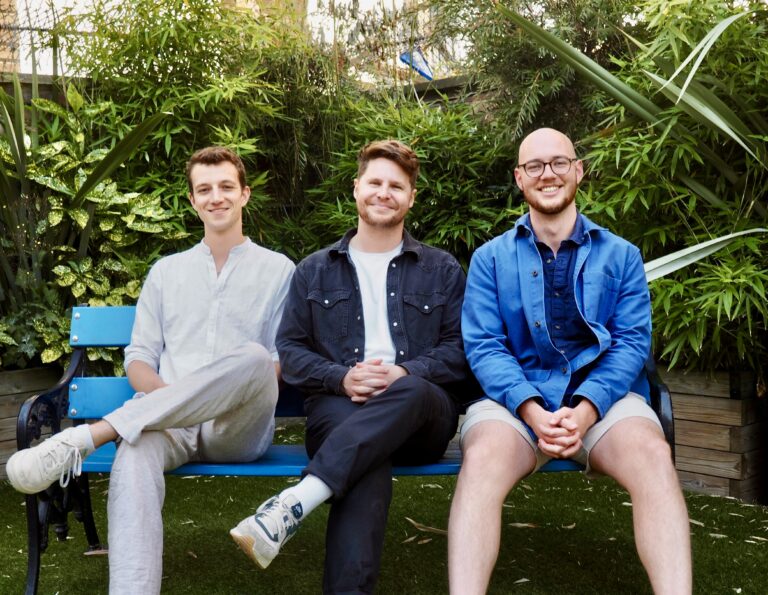
Profiles
Cocoon: Closing the Loop to Decarbonize Steel & Cement in Sync
Global construction is booming as steel and concrete makers race to cut emissions. Yet, new cleaner steel mills inadvertently deprive concrete of a key decarbonizing ingredient. Cocoon turns electric steel mill waste into a viable green alternative that aims to replace up to half of the cement used in concrete. All while creating new revenue for steelmakers and accelerating both industries' green transition.
Aug 7, 2024
Transforming Industrial Emissions with Waste-to-Value Solutions
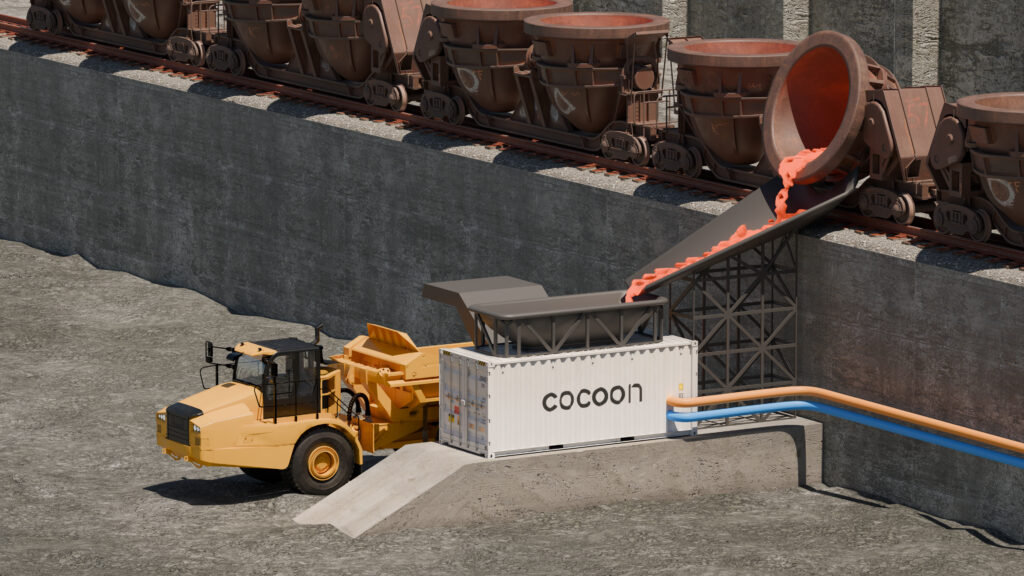
Global construction is set to boom over the next 40 years. It’s estimated to hit the equivalent of building a new New York City every month. This surge creates a challenge: steel and cement, essential for these projects, already contribute 14-15% of global CO2 emissions. All of this new construction aims to accommodate urban population growth and demand for clean infrastructure. However, it could also cause emissions to skyrocket.
Eliot Brooks, CEO of Cocoon, explains: ‘We want to enable tomorrow’s builders to construct critical infrastructure for the energy transition and better living. However, the materials needed to build that future are among the biggest contributors to climate change. That means we need to scale lower emissions building materials as quickly as possible.”
Moving Forward Faster, Together
Cocoon’s cofounders, Will Knapp, Eliot Brooks, and Freddie Scott, met at Carbon13, a climate-focused entrepreneurship program. The three hit it off, realizing their complementary skill sets would mean they could drive rapid progress working together. While flexible on the company idea, they were steadfast that it needed to deliver impact as soon as possible.
While exploring various climate solutions, the team identified a critical challenge in cleaning up concrete production. The steel industry’s shift to cleaner electric arc furnaces (EAFs) has created an unexpected problem. It’s eliminating a crucial material for low-carbon concrete: supplementary cementitious material (SCM). SCM is a waste byproduct of steelmaking used to replace cement in concrete, significantly reducing its carbon footprint. In the U.S., where 70% of steel now comes from EAFs, the United States Geological Survey found a shortage of slag, which has increased the price per ton by 100% since 2017. As more steel plants switch to ‘green steel,’ the shortage of SCM will continue to stall concrete decarbonization.
Cocoon’s Chief Science Officer, Will, previously studied carbon sequestration through mineralization. Yet, he found limited impact potential due to the carbon market dynamics. The team decided to leverage Will’s geology expertise to fix a broken link between the steel and concrete industries. Freddie, Cocoon’s Chief Technology Officer, sums up the dilemma: “We’re in a situation where cleaner steel inadvertently hampers cement’s decarbonization. Our solution bridges this gap, enabling both industries to decarbonize in tandem.”
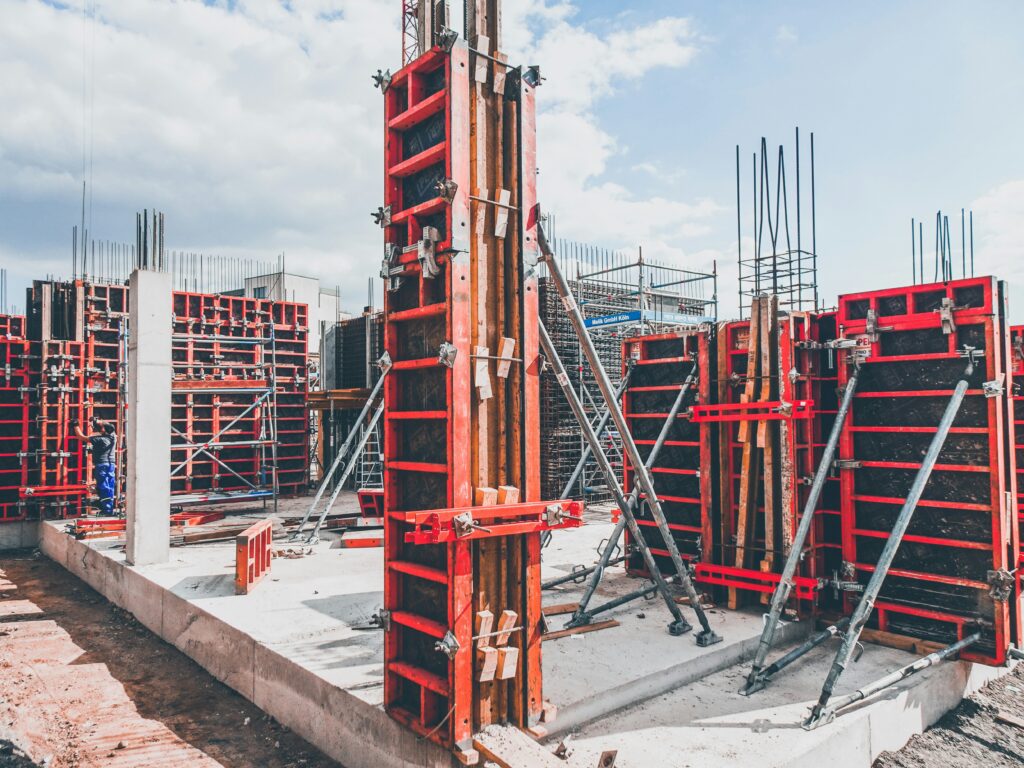
The Future of Sustainable Construction
Cocoon’s approach draws inspiration from historical practices while addressing modern challenges in construction. Using steel byproducts in concrete has been common. Eliot shares how, after World War II, the British needed to maximize resource efficiency and supply enough affordable building materials for post-war reconstruction. They found steel waste could replace cement, a key source of emissions in concrete. Cocoon is reviving this circular approach for lower-emission steel and concrete production.
We can put a Cocoon plant on every electric steel mill within ten years.
Eliot Brooks, Cofounder and CEO of Cocoon Carbon
Cocoon’s solution is elegantly simple. They turn a byproduct of electric arc furnaces (electric steel mill waste) into a replacement for the blast furnace slag. This creates a win-win for both industries. Steelmakers find a new revenue stream for their byproduct without changing their established processes. “Steel making has been perfected, we don’t want to change it,” says Freddie. “Instead, we add a modular unit at the end of the process. It turns waste e-slag into a valuable product. This process also captures and stores CO2, further reducing on-site emissions.”
For concrete producers, Cocoon restores access to a critical material needed for their own decarbonization. Generally, blast furnace SCM can replace anywhere from 30-95% of cement in concrete. Cocoon targets 50% cement replacement in concrete using their green SCM material. This could significantly cut emissions while the industry develops and standardizes cement alternatives over the next decade.
Eliot emphasizes the scalability of this approach: “We can put a Cocoon plant on every electric steel mill within ten years. This isn’t about scaling up a new process or developing an alternative to ordinary Portland cement. The material we need to have an impact already exists, the logistics networks are established, and there’s growing customer demand.”
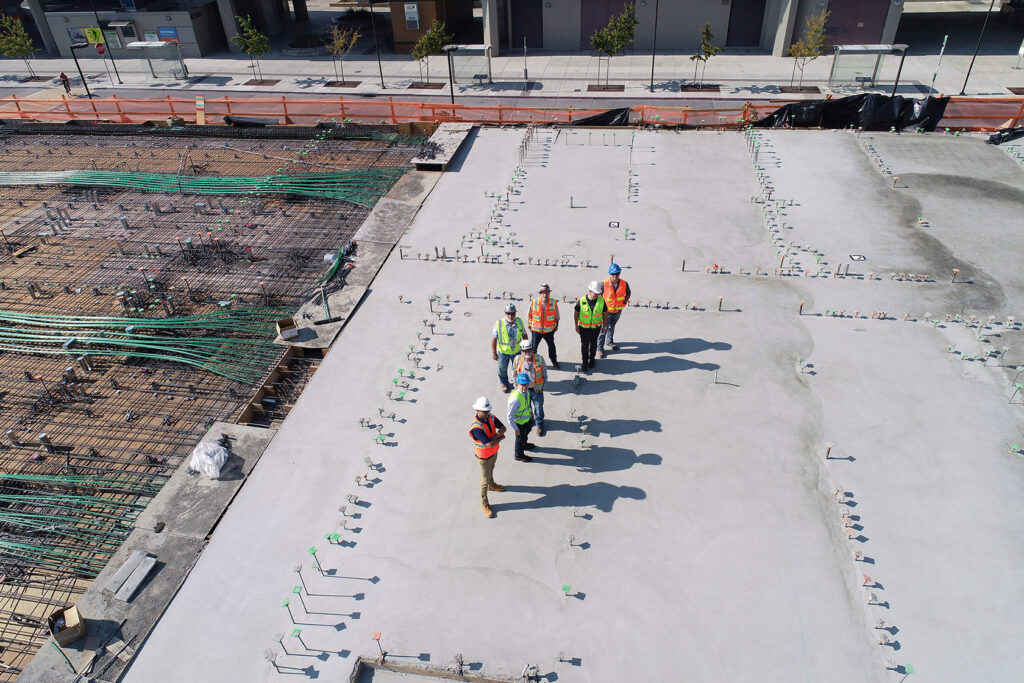
A Commercially Viable Path to Decarbonization
Cocoon offers commercial viability and scalability for a tricky climate problem. By delivering a valuable product with existing demand, Cocoon can build a business outside the voluntary carbon market. Using modular units, about the size of a shipping container, allows for low CapEx, quick market entry, and easier scaling than other approaches that disrupt steel plant operations. Evaline Tsai, from Gigascale adds: “Cocoon’s solution could speed up industry transition. It works with existing, scaled processes and requires minimal changes, helping both industries decarbonize cost-effectively.”
The team has gained impressive momentum too. In just 15 months, Cocoon built multiple prototypes, raised $5.4 million, and secured a UK plant agreement. They’re also planning a demo by the year backed by $1 million in Innovate UK grants. With the core technology proven, the next step is de-risking at a pilot scale.
Governments and business demand for green steel and concrete is expected to increase as producers face pressure to cut emissions. Cocoon is offering both a feasible solution, and even a potential profit boost for steelmakers who electrify. As Will muses, “If we assess the full impact, we might only decarbonize concrete by 20-40%. But looking at the potential to accelerate steel decarbonization, the impact is much greater.”
Global construction will not halt until new materials are created. Cocoon offers a pragmatic transition technology to bridge the gap between increasing demand and emissions reduction. By repairing a broken link in the circular economy, Cocoon enables more sustainable practices today while paving the way for a clean built environment tomorrow.